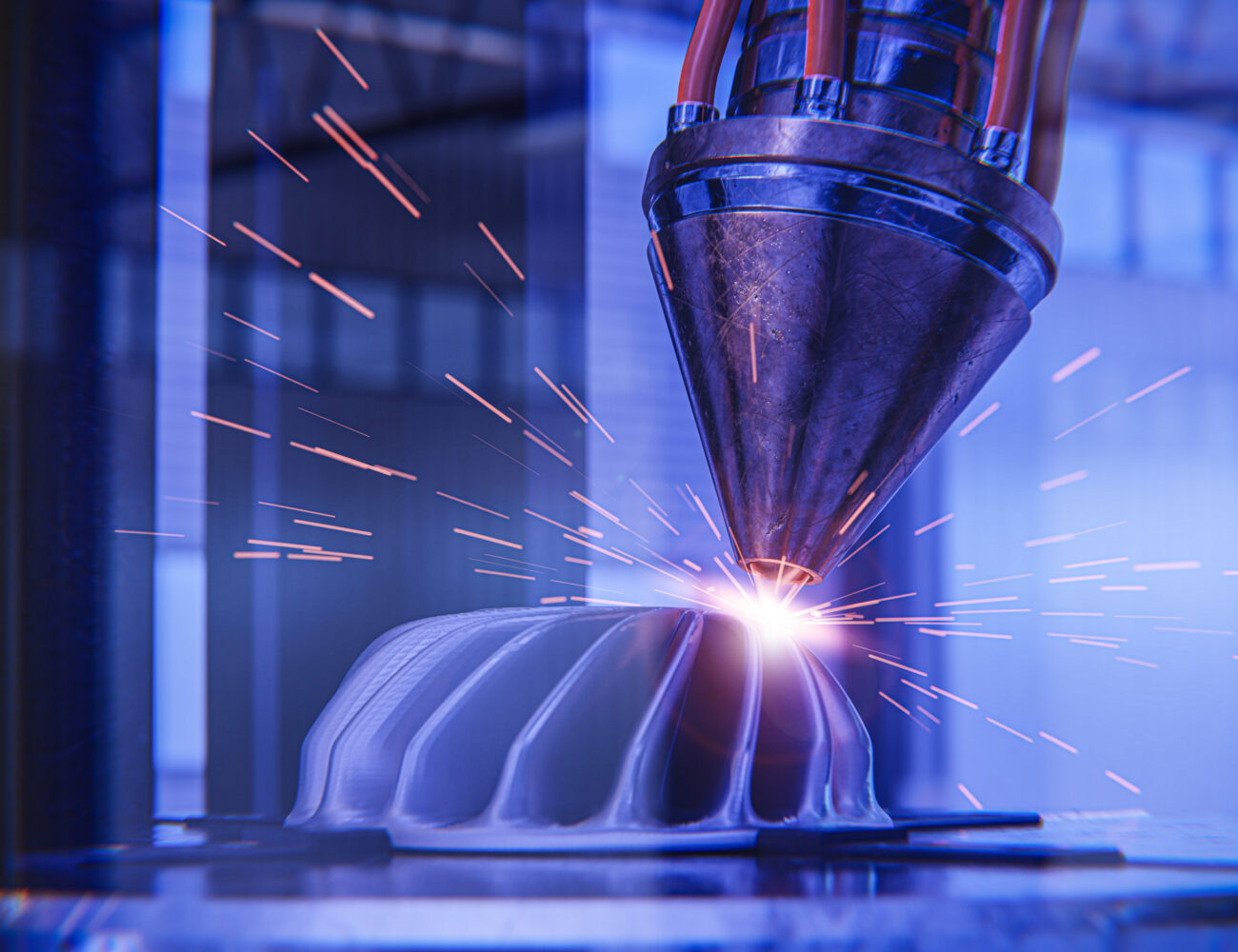
Peek2Space
Start of the project: 01-12-2023
End of project: 30-11-2025
GENERAL OBJECTIVE :
High-performance polymer materials are in great demand in various high-tech sectors such as aeronautics, aerospace, maritime, automotive and medical, and energy (batteries, PEMFC cells) for, among other things, their weight, high strength and chemical and mechanical resistance.
At the same time, these sectors are showing great interest in additive manufacturing, exploring its advantages in terms of design freedom, reduced costs and resources, and reduced environmental impact. In many cases, the heavy (metallic) materials traditionally used could be (partially) replaced by lightweight materials such as polymers, with identical or even improved structural and/or functional properties. The combination of design freedom and alternative materials is of particular interest to the aerospace industry.
High-performance polymer materials and additive manufacturing equipment are becoming increasingly available, with improved quality for the former and greater precision, speed and reliability for the latter.
However, the overall performance of the manufactured object lacks a certain maturity compared to that of conventional materials. In general, this can be attributed to the nature (chemical/physical) of the high-performance polymer, the design and the manufacturing parameters.
Many companies (such as Sabca, ESA,....) have shown great interest in objects produced in PEEK (a high-performance polymer) using additive manufacturing.
An important aspect of polymers in general is that these materials can be functionalised using specific additives to improve the (bio)chemical and/or physico-mechanical properties of the material or object.
PEEK is often chosen by the aerospace industry not only for its light weight (compared with conventional materials such as titanium), but also for its structural rigidity and low outgassing. However, the problems raised by the industry are often linked to thermal management and electromagnetic shielding. By loading PEEK with specific additives (SIRRIS), the consortium believes it can improve the above-mentioned problems. In addition, plasma treatment of the filled PEEK (MateriaNova) could improve adhesion during the additive manufacturing process (SIRRIS) and therefore improve the overall properties of the final object, which can be characterised by the conventional means used on polymer materials (Materia Nova).
A consortium between Materia Nova and Sirris has been set up to :
- Meet the needs of the above companies in terms of the overall performance of PEEK objects
- Improve the functionality of PEEK by means of functional fillers (Sirris)
- Solve problems linked to the chemical and physical nature of PEEK (Materia Nova and Sirris)
- Optimising PEEK additive manufacturing parameters (Sirris)
- Evaluate the performance gain (Materia Nova)
- Propose demonstration parts (industrial support committee)
MATERIA NOVA'S MISSIONS :
Development of an atmospheric plasma torch solution to be integrated into the printing process to improve adhesion between the strands already deposited and those being extruded. Optimisation of the exposure conditions and the gas mixture in order to create radicals on the surface of the polymers and thus promote the creation of covalent bonds.
Project leader: Sirris
Contact Materia Nova : thomas.godfroid@materianova.be
Total budget : 595518.04€
Funded budget : 446638,53€
Budget Mano : 295839,45€